Custom Meat Stick Singulation System
Project Overview
CHL Systems worked with a leading meat snack producer to upgrade their packaging process for individual meat sticks. Our customer had secured a robotic pick-and-place system to place the meat sticks into their packaging but needed a crucial solution for indexing and delivering the bulk products to the robot for picking. Drawing on our expertise in automation solutions for the snack food industry, we provided our customer with a custom-designed automated meat stick singulation system.
Key Challenges
- Providing a solution for delivery and indexing of bulk products
- Integrating with robotic pick-and-place packaging system
- Maintaining a compact footprint to fit within space constraints
- Accommodating two different product sizes
- Achieving a delivery rate of 360 pieces per minute
- Meeting strict food safety standards
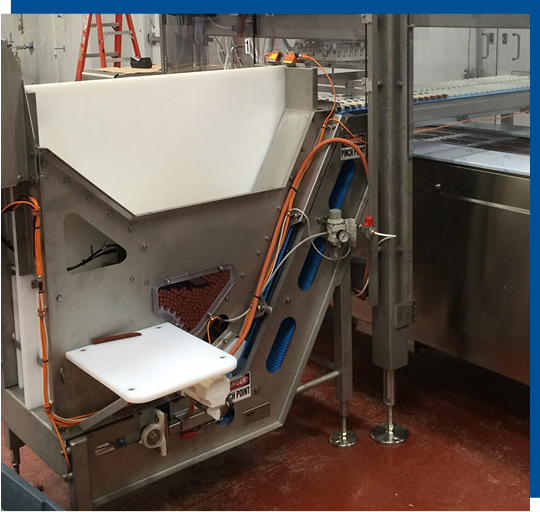
CHL Systems’ Solution
CHL Systems engineered and fabricated a custom singulation system that indexes 1-oz. and 0.5-oz. meat sticks into precise lanes, delivering them from a bulk hopper to a pick-and-place robot at a rate of 360 pieces per minute.
Key Features
Key features include:
- Servo-driven star-wheel feeding mechanism
- Precision-timed conveyor with specialized flight pockets to match robot configuration
- Bulk hopper with 10-minute product capacity
- Coordinated three-axis servo control system
- User-friendly operator interface
- Washdown-duty components for food safety compliance
- Dual-format capability handling both 6.5″ and 3.25″ product lengths
Results
The system achieved:
- Consistent feed rate of 360 pieces per minute
- Precise 24-piece indexed presentation for robotic picking
- Compact design utilizing a star-wheel feeding mechanism
- Reduced manual handling requirements
- Flexible operation supporting multiple product sizes
- Enhanced operational efficiency through automated singulation
- Seamless integration with existing packaging equipment
The CHL Systems Advantage
CHL’s engineering team followed a methodical development approach throughout the innovation process.
Conducted initial concept testing with multiple feeding methods.
Refined the star-wheel and hopper configuration through iterative testing.
Implemented error detection to ensure consistent product presentation.
Performed prototype validation using wooden dowels and the actual product.
Developed specialized programming to coordinate mechanical movements.
This innovative solution not only met the immediate needs of the meat snack producer but also established a versatile platform applicable to various product types in the packaging industry. The system’s success demonstrates CHL Systems’ ability to deliver efficient custom automation solutions while maintaining high standards for food safety and operational reliability.