Candy Packaging Line
Upgrade
Project Overview
CHL Systems successfully executed a comprehensive upgrade of three packaging lines for a major candy producer, demonstrating our expertise in turnkey solutions for the food manufacturing industry. This complex project involved the simultaneous upgrade and integration of the three lines (Lines 1, 2, and 7), each presenting unique challenges and requirements.
Key Challenges
- Increasing throughput and improving packaging efficiency
- Minimizing disruption to ongoing production
- Integrating multiple vendors’ equipment and components into one seamless operation
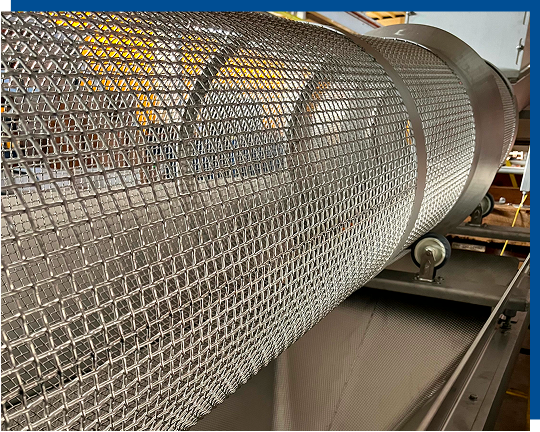
CHL Systems’ Solution
CHL Systems provided a turnkey solution, including engineering, design/build, integration, and installation.
Key Features
For Line 1, CHL engineered and installed an entirely new system, from the mezzanine level down to the packaging and palletizing equipment, including:
- Engineering, manufacturing, and installation of a new auto dumper, bin conveyor, and rotary screen system.
- Integration and installation of a new filler, metal detector/check weigher, case packer, and shrink wrapper.
- Design and installation of a comprehensive case conveyor system, including a new spiral elevator and overhead conveyor span to the palletizing room.
Line 2 saw a significant upgrade with the integration of new equipment into the existing setup, including:
- Integration of new filler, metal detector/check weigher, case packer, and shrink wrapper with existing equipment.
- Installation of new “S” configuration carton conveyor.
- Upgraded transfer system at the mezzanine level for improved efficiency
For Line 7, CHL focused on strategic upgrades to improve the line’s overall performance, including:
- Integration of a new filler and metal detector/check weigher.
- Coordination of retooling of existing Aagard equipment.
- Design and installation of a new carton elevating system to replace the existing elevator.
Results
- Seamless integration of equipment from multiple vendors
- Custom conveyor systems designed for efficient product flow
- Upgraded control systems and integration
- Flexible installation schedule to minimize production downtime
- Increased packaging line efficiency and throughput
- Improved product handling and transfer between equipment
- Enhanced overall line performance with modern, integrated equipment
- Minimal disruption to ongoing production during installation
The CHL Systems Advantage
Turnkey project management from engineering to final installation of all three lines
Expertise in integrating equipment from various vendors into a cohesive system
Flexible installation approach, including phased implementation and weekend work
Expertise in seamlessly combining new and legacy systems
Custom engineering solutions to address unique layout and space constraints
On-site support during installation and commissioning to ensure smooth startup
This project showcases CHL Systems’ ability to handle complex, multi-line packaging upgrades while integrating new and existing equipment. By providing a turnkey solution, CHL ensured that all aspects of the project were coordinated and executed efficiently. As a result, the candy producer experienced a significant improvement to their packaging capabilities, with increased efficiency, improved product handling, and enhanced overall line performance. This project underscores CHL Systems’ position as a leader in providing innovative, integrated solutions for the food manufacturing industry.