Automated Case
Packing System (ACPS)
Project Overview
CHL Systems implemented a sophisticated automated case packing system (ACPS) for a leading global chocolatier, transforming their manual packaging operations into a state-of-the-art automated solution. The project centered on a Bindler shell moulding line, where chocolate products in plastic trays required careful handling and precise packaging for work-in-process (WIP) storage.
The system was designed to handle reusable packaging components, including plastic cases and protective materials, creating a sustainable and efficient packaging cycle. Upon WIP usage, the cases, trays, and padding materials are returned to the packing line for reuse, maximizing resource efficiency.
The project was executed in two distinct phases, allowing for thorough testing and validation of critical components before full implementation. This approach minimized production disruption and ensured system reliability upon deployment.
Key Challenges
- Convert 6-person manual packaging operation to fully automated system
- Implement multi-robot handling system for precise product placement
- Maintain capability for manual operation during maintenance
- Enable system flexibility for alternate production routing
- Integrate with existing metal detection and labeling systems
- Install advanced vision systems for quality control
- Implement ergonomic pallet handling stations
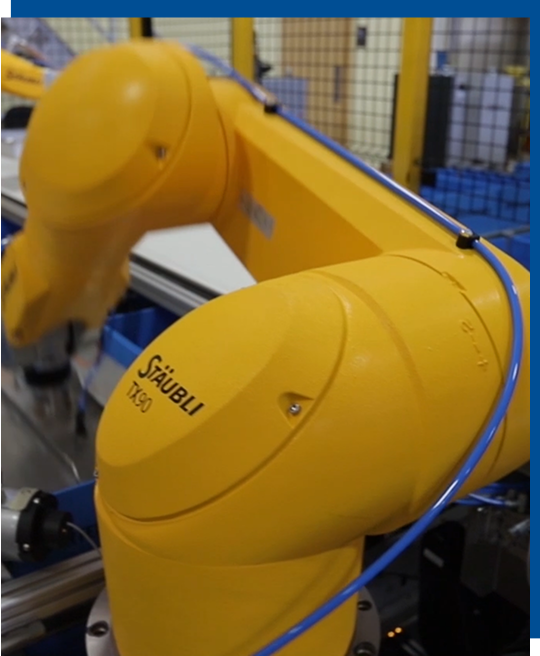
CHL Systems’ Solution
Key Features
CHL Systems designed and implemented a state-of-the-art automated case packing system including the following components:
- 4 Staubli SCARA robots with food-grade lubricants
- 2 robots for tray handling
- 2 robots for protective sheet insertion
- 1 palletizing robot
- Cognex vision system for quality inspection
- Automatic case erector and sealer
- Integrated conveyor system
- Dual pallet loading stations
Technical Highlights
CHL Systems designed and implemented a state-of-the-art automated case packing system including the following components:
- Processing rate: 24 trays per minute
- Case packing rate: 5 cases per minute
- Pallet configuration: 49 cases per pallet (7 rows x 7 cases)
- Pallet completion time: 9.8 minutes
- Case dimensions: 535mm x 345mm x 150mm
Key Benefits and Outcomes
Vision Integration:
- Cognex camera system implementation with specialized lighting
- Red external light and LED configuration to manage product reflections
- Real-time tray orientation verification
- Integration with robot control for precise placement
- Automated quality inspection for missing or defective chocolates
Quality Control:
- Automated rejection system with dedicated under-conveyor QC area
- Integration with existing metal detection system
- Automated weight verification system
- Label verification capabilities
- Real-time rejection tracking and storage capacity for up to 4 trays
Redundancy:
- Reduced-rate operation capability with only two robots
- Manual operation backup mode
- Dual pallet loading stations
- Multiple robot programming configurations
- Automated switchover between pallet stations
Flexible Operations:
- Dual-mode system design allowing both automated and manual operation
- Quick-changeover capability for maintenance periods
- Integration of portable bypass conveyors for alternative production routing
- Ability to disengage automation for Bosch candy wrapping machine connection
- Modular design allowing section isolation during maintenance
Efficiency Design:
- Space-optimized S-shaped conveyor configuration
- Strategic placement of robots for maximum throughput
- Ergonomic operator access points
- Crossover stairs between sheet feeders and case sealer
- Removable conveyor sections for flexibility
Safety Features:
- Robot cell guarding systems
- Light curtain implementation
- Automated case rejection capability
- Dedicated maintenance access points
- Safety-compliant pallet loading zones
The CHL Systems Advantage
CHL Systems provided a turnkey automated solution including advanced engineering, thorough testing, design/build, integration, and installation. Our two-phase approach to the project minimized production interruption and ensured system reliability.The success of this project demonstrates the effectiveness of a phased implementation approach, where thorough engineering analysis and risk mitigation preceded full system deployment. The resulting system met the immediate automation needs of our client and provided a foundation for future expansion and enhancement.
Phase 1: Engineering & Risk Mitigation
Phase 1 focused on comprehensive engineering analysis and risk mitigation strategies. The engineering team began with detailed layout planning, carefully considering spatial constraints and operational efficiency. Through rigorous equipment evaluation, the team selected Staubli robots for their precision and food-grade compatibility.
A significant milestone was the successful prototyping of custom end effectors, which underwent extensive testing to ensure reliable product handling. Robot programming achieved 50% completion, establishing core movement patterns and handling sequences.
The team conducted thorough validation testing of the PlastiCorr case handling system and protective material interactions. This phase concluded with detailed documentation and risk assessment reports, providing a solid foundation for implementation.
Phase 2: Implementation & Integration
Building on the engineering groundwork of Phase 1, Phase 2 marked the transition to physical system integration. The implementation process began with the assembly of major system components, including the robotic cells, conveyor systems, and safety infrastructure.
Controls programming expanded upon the initial robot programming, incorporating vision systems and implementing complex handling sequences. The team conducted comprehensive factory acceptance testing (FAT) to validate system performance under various operational scenarios.
Site installation followed a carefully planned sequence to minimize production disruption, culminating in full system commissioning. Throughout this phase, the team maintained flexibility to accommodate design refinements, such as modifying conveyor sections for improved accessibility and incorporating crossover stairs for enhanced operator movement.