Rib Line Trimming and Classifying Upgrades
Project Overview
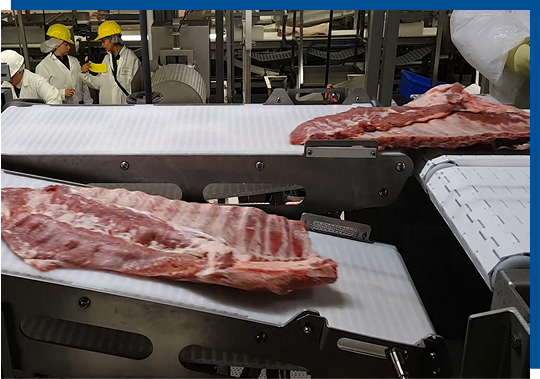
Phase 1: St. Louis Rib Line Upgrade
Custom Solution
CHL Systems engineered a comprehensive upgrade to the existing rib line, including:
- Modifications to the existing belly line
- Installation of a new elevated in-motion trimming line
- Implementation of an overhead conveyor system for various rib types
- Integration of an advanced classifying and packaging system
Key Features
- Custom-designed conveyors with precise spacing and timing
- In-line brisket saws with positioning lasers for accurate cuts
- Vande Berg in-motion scales for weight-based classification
- Integrated controls system for seamless operation
Results
- Increased conversion rate of spare ribs to St. Louis style ribs to 32 pieces per minute
- Improved system throughput
- Enhanced classification accuracy with 6 weight ranges for St. Louis ribs
- Optimized packaging process for various rib types and byproducts
Phase 2: Baby Back Rib Line Upgrade
Custom Solution
CHL Systems developed an additional trimming line and upgraded the rib classifying system, including:
- New high-precision scale infeed and conveyor system
- Advanced classifying conveyor with pneumatic product diverts
- Custom-designed rib trimming station with integrated scales
- Ergonomic operator stands for improved workflow
Key Features
- Vande Berg scale conveyor with 0.01 lb. accuracy
- 8-position pneumatic divert system for precise product sorting
- Customized trim and takeaway conveyors
- Height-adjustable, ergonomic operator stations
Results
- Increased baby back rib processing capacity to 36 pieces per minute
- Improved grading accuracy and consistency
- Enhanced ergonomics and efficiency for trimming operations
- Seamless integration with existing production lines
The CHL Systems Advantage
By partnering with CHL Systems, our customer significantly improved their rib processing operations, driving efficiency, quality, and throughput. This project exemplifies our ability to deliver innovative, custom-engineered solutions that provide lasting value to our clients in the food processing industry.
Custom Engineering
Each solution was tailored to the client’s specific needs and facility constraints.
Comprehensive Service
From initial design to installation and start-up support, CHL provided end-to-end project management.
Attention to Detail
Features like ergonomic design and precise controls showcase CHL’s focus on every aspect of the solution.
Continuous Improvement
By building on previous upgrades, We demonstrated our commitment to evolving solutions as client needs change.
Integration Expertise
New systems were seamlessly integrated with existing equipment and processes, minimizing disruption.