Efficient Patty Line
Automation
Project Overview
CHL Systems engineered and manufactured a custom patty handling conveyor system for a leading beef processor’s patty production lines. The project aimed to efficiently transport and merge patty slugs from multiple forming machines onto a single conveyor line, accommodating different patty sizes and production rates.
Key Challenges
- Handling two patty sizes: 2 oz. (6 stacks of 14 tall) and 4 oz. (6 stacks of 8 tall)
- Managing high-speed production rates of 6.25–6.28 slugs per minute from each forming machine
- Merging patty slugs from multiple lines onto a single conveyor system
- Ensuring smooth transitions between conveyors to maintain patty integrity
- Integrating with existing equipment and meeting specific height requirements
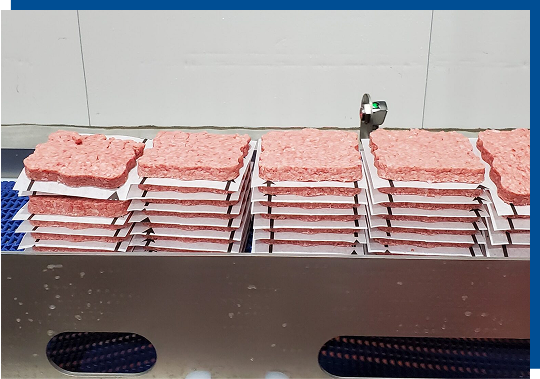
CHL Systems’ Solution
Key Features
- Multiple takeaway conveyors with precise dimensions and inclines
- Innovative shuttle conveyors for efficient patty slug transfer
- Meter conveyors for controlled product flow
- Advanced control system with PLCs for seamless operation
- Strategic placement of photo eyes for accurate timing and product detection
- VFD-controlled motors for speed optimization
- Pneumatic systems for shuttle conveyor actuation
Results
- Automated handling system processes 6.25 slugs per minute from each forming machine
- Dual product capability handles both 2oz and 4oz patties without line modifications
- Sanitary design meets stringent food safety requirements
- Smart controls enable precise product tracking and transfer timing
- Reduced maintenance requirements through robust mechanical design
The CHL Systems Advantage
Through innovative engineering and precise execution, CHL Systems delivered a transformative solution that revolutionized the client’s patty handling operations. The custom-designed system not only met the immediate production challenges but established new benchmarks for efficiency and reliability in food processing automation. By implementing advanced control systems and sophisticated product handling mechanisms, CHL Systems created a seamless integration between existing equipment while significantly reducing product damage and operational downtime.
This project exemplifies CHL Systems’ commitment to delivering customized automation solutions that drive operational excellence and sustainable value for food processing clients.
By partnering with CHL Systems, our customer significantly enhanced their patty production capabilities, setting a new standard for efficiency and quality in their operations.